Advantages of Rubber Suspension Bushes
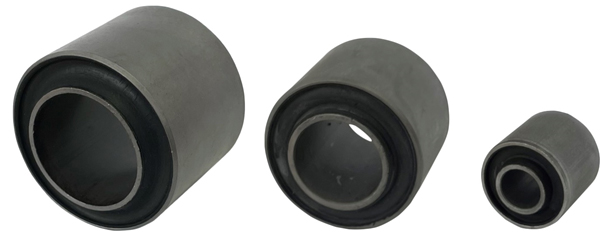
Rubber Suspension Bushes (also known as Rubber Bushings) have three main constituent cylindrical components. The individual components include the inner metal sleeve, the middle rubber section, and the outer metal sleeve, with all three concentric to each other. The inner sleeve and outer sleeve are typically manufactured from steel tube and the rubber section normally natural rubber which provides a high level of driver/operator comfort and extended fatigue life. In addition, it has become common practise for aftermarket sports vehicle suspension upgrades to utilise polyurethane rubber. Polyurethane Bushes achieve higher stiffness due to their higher hardness, thereby giving the driver a firmer ride and be more in tune with the road surface.
The AV Industrial Products Ltd range of suspension bushes provide maintenance free multi-directional movement whilst transmitting forces within machine links. Click here to view our Rubber Suspension Bushes.
There are many applications for the AV Industrial IOS rubber bush, which include;
- Vehicle Suspension Arms
- Panhard Rods
- Vehicle lateral load transfer links
- Off Highway Vehicle Control Links
- Cab Mounts
- Torque control arms
- Wind Turbine Bushes (Gearbox Bushes / Generator Bushes)
- NVH reduction
Further information on the standard range of Rubber Suspension Bushes can be found here. In addition, we can also manufacture custom sizes to suit your application. Contact us at mail@avindustrialproducts.co.uk with your require dimensions.
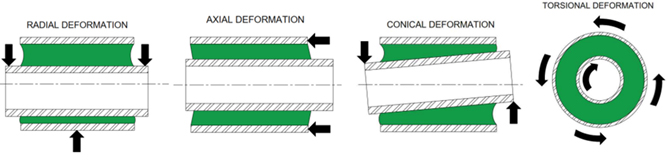
Rubber Bushings for Vehicle Suspension
NVH is an acronym for Noise, Vibration and Harshness. The rubber bush is particularly effective at reducing the transfer of knocks, road noise, etc within vehicle suspension applications. The rubber middle section assists with the noise dampening and impacts from the road wheel. Those noises and impacts are dampened between the outer metal sleeve and inner metal sleeve providing a much smoother and quieter operator experience.
As well as the much-improved NVH considerations, the AV Industrial IOS rubber bush also allows the multi-directional movement and smoother load transfers. With the inner sleeve metal clamped into the vehicle chassis and the suspensions arm fixed to the outer sleeve metal, they can articulate against each other. As the road wheel travels over undulating road surfaces the movement is transferred from the wheel via the bearing hub, into the chassis via the suspension arm, where the rubber bush is located.
This suspension movement induces a torsional angular movement of the inner sleeve relative to the outer sleeve. This relative angular movement of a rubber bush can be determined and designed accordingly. Factors that affect the permitted relative angular movement of a rubber bush include:
- Length of rubber
- Outer diameter of the rubber
- Inner diameter of the rubber
- Rubber Modulue
If the permitted angular movement exceeds the bush design limits, then it could cause premature failure of the rubber.
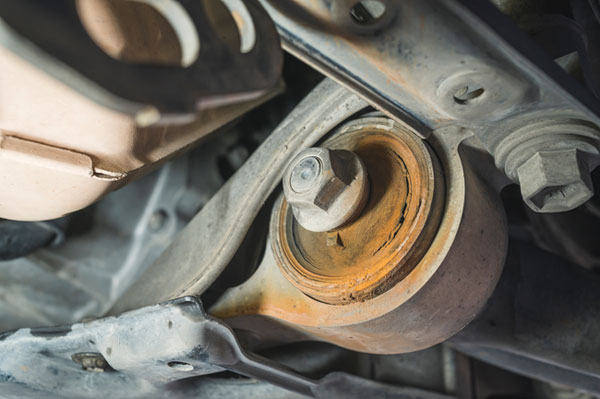
If the road wheel takes an impact from the tarmac surface, this could induce a radial impact load onto the rubber bush. The radial load intensity that the rubber bush can withstand may also be determined from several design criteria. Rubber bushes are designed to withstand other load directions that include axial and conical.
All of the above design factors can be determined and refined following a consultation with the AV Industrial Products’ engineering team. The AV Industrial Products’ engineering team have vast knowledge with the design, application and selection of rubber bushes.
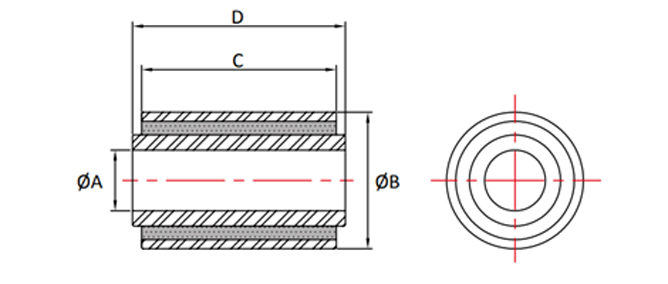
Additional Technical Information
The AV Industrial Products IOS Rubber Bush Metals are machined and prepared ready for the rubber bush manufacturing process. Please review the AV Industrial Products Home Page for further detailed information regarding this.
The outer sleeve metal thickness can be according to the customer requirements however if not specified there are standard wall thicknesses. The outer sleeve metal is generally inserted into a mating housing, whereas the inner sleeve metal is normally clamped into position. For this reason the inner sleeve metal generally has a thicker wall section to withstand the bolt clamp loads, compared with the outer sleeve.
Normally the outer metal is an interference fit into the respective housing. The outer sleeve outer diameter normally has a fine tolerance suitable for fitment into the housing. There are different levels of interference fit and the AV Industrial engineering team can discuss these with you.
The tolerance of the inner sleeve inner diameter is not normally as critical as the outer sleeve outer tolerance, due to the fitment of a standard bolt. However, it is also possible to install an interference fit pin into the inner sleeve inner diameter and fine tolerances can be discussed with the AV Industrial engineering team.
The metal inner sleeve length and the metal outer sleeve lengths are generally according to standard machining tolerances, but AV Industrial Products can provide other non-standard length tolerance requirements. Again, these can be consulted with the AV Industrial Products engineering team.
Following the rubber moulding process, the middle rubber section may contract as the bush temperature cools. This rubber contraction induces stresses within the rubber and can change the rubber stiffness characteristics and ultimately affect the service life of the bush. AV Industrial Products therefore have developed a post-moulding pre-stress process, which can greatly improve the service life of the product compared to other competitor products.
AV Industrial Products offers rubber bushes in a wide variety of dimensions and rubber profiles to suit the vast majority of applications and including the most demanding of customer requirements. AV Industrial Products offers many different rubber bush solutions for the most diverse applications.
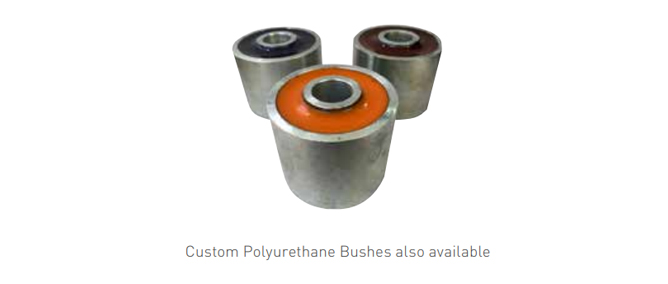
Rubber Bush Testing
AV Industrial Products can offer both static and dynamic testing to meet the client specifications. Static tests are utilised to measure the mechanical properties such as stiffness, whereas Dynamic tests are available to enable accelerated testing of the rubber bush. Accelerated testing allows the rubber bush to be subjected to the demands of the application via a controlled regime. The test regime subjects the rubber bush to loads and/or angular movements over a number of cycles, typically in the order of 1 million. The purpose of the dynamic testing is to ensure that the rubber bush can withstand the application specifications.
Dynamic testing is also used to perform back-to-back testing, fatigue testing and endurance testing. These tests can be utilised to demonstrate that the AV Industrial products’ rubber bush is identical (or better than) a competitor’s rubber bush.
AV Industrial Products has the knowledge and ability to propose, manufacture, test and supply the rubber bush to suit the most arduous client specifications. Please do not hesitate to contact or enquire here with any rubber bush question. We will be very pleased to assist with your requirements.